Transferred arc mode
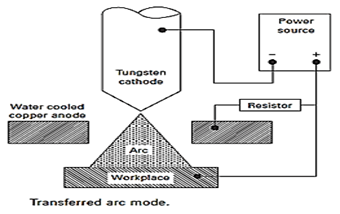
In the transferred arc mode, the arc is maintained between the electrode and the workpiece. The electrode is usually the cathode and the workpiece is connected to the positive side of the power supply. In this mode, a high energy density is achieved and this energy is efficiently transferred to the workpiece.
Non-transferred arc mode
- In the non-transferred arc mode of operation, the power supply is applied between the electrode and the constricting orifice. The electrode is usually connected to the negative side of the power supply and, for this reason; the orifice is referred to as the anode.
- In this mode, very little energy is transferred to the workpiece and its main use is as a ‘pilot’ arc which enables the main transferred arc to be established rapidly.
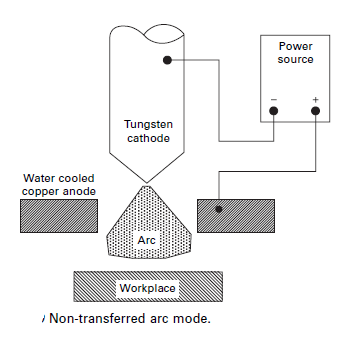
Equipment requirements:
- The basic equipment requirements for the plasma welding system are slightly more complex than either the conventional or dual-gas GTAW system.
- They consist of a welding power source, a control unit and a plasma torch.
- A power source with a direct current (DC) output is normally used (although it is possible with suitable equipment to use AC for aluminium alloys and variable polarity or ‘square wave’ AC units referred to above have been developed as plasma power supplies).
- The constant-current static volt–amp output characteristic used for GTAW power sources provides a suitable main arc supply.
- The control unit which usually contains the non-transferred pilot arc supply, the gas controls and the arc ignition system may take the form of an ‘add on’ box or may be built into the main power supply
The torch is slightly more complex than a GTAW torch.
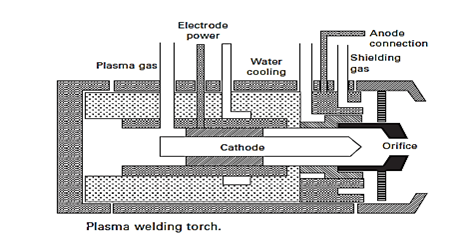
- It must have provision for cooling of the replaceable copper constricting orifice, supply of plasma gas, and a separate supply of shielding gas.
- The non-consumable electrode material is usually thoriated tungsten. As in GTAW, the process may be used without added filler (autogenous welding) but, if filler is required, this is usually added to the leading edge of the molten pool.